How Electric Turbochargers Are Changing Internal Combustion
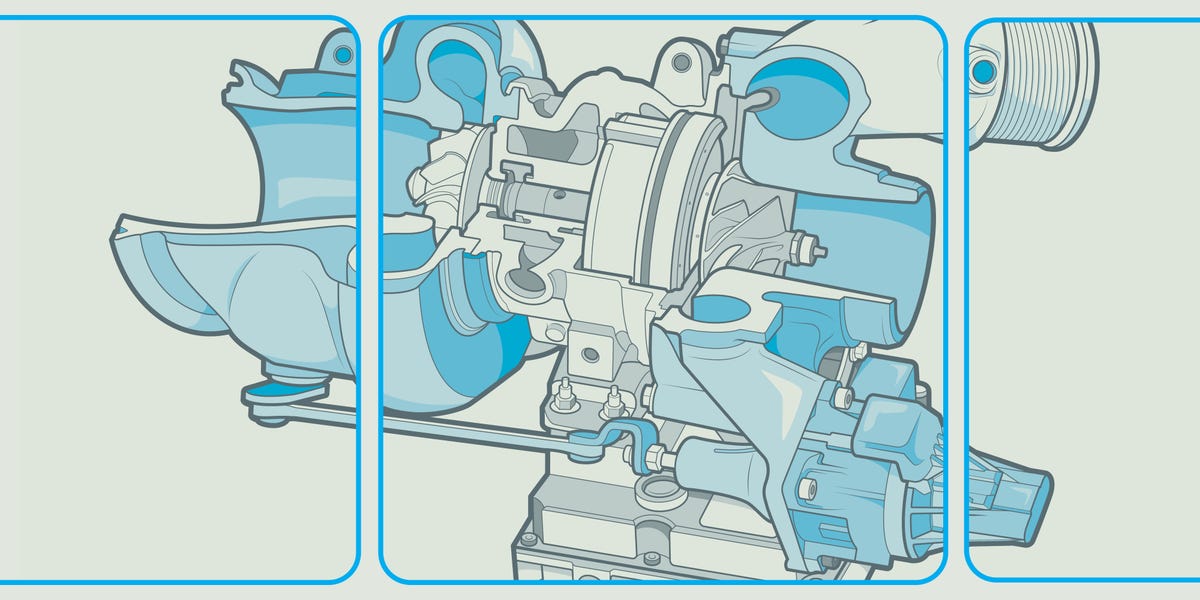
Now more than ever, automotive engineers have to chase efficiency wherever they can. In an internal-combustion engine, a turbocharger is a great way to boost power and efficiency for an engine of a given displacement, and over the last decade we’ve seen a proliferation of downsized, turbo engines replacing larger naturally aspirated units. Yet, the turbocharger itself is far from perfect.
A turbocharger is a crude device. It takes a while to spool up, the spool is entirely dictated by the flow of exhaust gasses, it wastes a lot of those exhaust gasses, and it’s hot. Plus a traditional turbo can only be operated well below its maximum speed, because if it exceeds this, damage to the turbo and/or engine can occur.
An electric turbocharger can solve a lot of these problems, and more.
Let’s dip into a quick, perhaps unnecessary, sum-up of turbocharger basics. Within the snail-shaped housing are two turbines on either side connected by a small shaft. Exhaust gasses blow on one turbine, which in turn spins the other called the compressor wheel. The compressor wheel increases air density in the intake, boosting engine power. Fresh air also feeds the compressor, and typically, the air from the compressor goes through an intercooler of some sort to reduce intake air temperature. On the exhaust side, there is usually a valve that opens and sends excess air downstream to the rest of the car’s exhaust system once the turbine is up to a desired speed. This is called the wastegate.
An electric turbocharger is basically just a regular turbocharger with a motor attached to the turbine shaft. Simple in concept, difficult in execution, filled with possibilities. “It brings another degree of freedom, says Craig Balis, CTO at Garret Motion, in an interview with Road & Track. “Automakers can use it for power, they can use it for efficiency, they can use it for emissions, they can use it for drivability.”
Garrett has been in the turbo business for decades, and it was the first to bring an electric turbocharger to the market. Mercedes-AMG is the first automaker to offer it, in both the C43 and C63, which pair an e-turbo with AMG’s 2.0-liter M139 for 402 and a staggering 476 hp, respectively. The C63 has the most power-dense engine on the market today, with 251 hp/liter, and because enough is never enough, the four-cylinder is augmented by a plug-in hybrid system for 671 hp.
It’s easy to think that the sole job of an electric turbocharger is to reduce lag. That’s what I thought, and indeed, that is a huge benefit of its use. In very simple terms, a larger turbocharger—with larger turbine and compressor wheels—can force more air into an engine, making more power, but the bigger you go in turbo size, the longer it takes to achieve the target boost level. Add an electric motor to the shaft, however, and you can get the whole thing up to maximum speed without waiting on exhaust gasses. (Turbo lag cannot be eliminated but it can be reduced to such a small amount that it’s inconsequential.)
Balis prefers to use the term transient response—what happens when you press the accelerator—rather than turbo lag. He points out that improving transient response not only helps with drivability, but emissions too. “You’re able to control the air that goes into the engine more precisely, matching it with the fuel and the demand on the engine.”
Then, there’s the efficiency an e-turbo brings. An electric motor can spin in two directions, and spun in reverse, it can act as a generator. In hybrid and battery-electric vehicles, the slowing of the motors can be used to slow down the car while putting energy into the battery. On a much smaller scale, you can do the same thing with the motor of an electric turbo. “The funny thing about the turbo is over various drive cycles, typically it can be energy neutral,” Balis says. “Meaning you can generate as much as you use. It’s at different points in time, but over various drive cycles, it can become energy neutral, or even energy positive.”
Garrett’s electric turbo still uses a wastegate, though the more precise level of boost control means less exhaust gas is wasted, and thus, a smaller wastegate can be used. Having a motor on the shaft means that the precise speed of the turbo is always known. Typically, a modern car’s ECU estimates the speed of the turbo and uses the wastegate to manage boost pressure, but leaves a huge margin for error for safety and durability. This leaves performance on the table for a given turbocharger size. If you know the exact speed of your turbo, however, you can run it much closer to its operating limit without fear of exceeding it. It’s not a benefit unique to e-turbos—Ferrari and Nissan both use traditional exhaust-gas turbochargers with speed sensors—but it’s important to note.
Garrett started working on e-turbos 20 years ago, but found that they simply weren’t viable with 12-volt electrics. Balis says you could only have a 3-kW motor on the shaft at the maximum, and even then, it was a big draw on the system. With the rise of higher-capacity electrical architectures, electric turbocharging became viable. Most versions of the current C-Class use a 48-volt “mild-hybrid” architecture, while the C63 uses an AMG-designed 400-volt plug-in hybrid system. Mercedes also decided that the new C-Class would only receive four-cylinder power. Electric turbocharging made a lot of sense here.
According to Jan Habermann, one of the engineers behind AMG’s application of e-turbos, the company wanted to give the C43 a more special engine than its predecessor, which used a V-6 shared with non-AMG products. The M139 is made by hand at AMG’s factory in Affalterbach, and while it can be found in AMG’s 45-series cars, those have 12-volt electrics, and thus, traditional exhaust-gas turbochargers. The C43 gets the e-turbo not for more power—the CLA45 S makes 415 hp to the C43’s 402—but for all the other benefits the hardware brings.
The C63 represents a different story. Its four-cylinder plug-in powertrain replaced a much-loved 4.0-liter V-8, and AMG knew it had to pack a huge punch. “[Going] hybrid has a lot of advantages,” Habermann says. “You can have a very small and fuel-efficient engine on one side; you can drive fully electric, and you have really insane performance, much, much, much better than the predecessor.” AMG felt that the C63 had to not only compete with traditional gas-powered super-sedans but with new, ultra-powerful EVs. (In a world where Kia sells a 577-hp version of the EV6, you can see the logic.)
To get the sort of power out of a 2.0-liter turbo four AMG was after, Habermann says that you’d have “turbo lag like hell” with a traditional turbocharger. The C63’s turbo has a compressor wheel diameter of 71 mm to generate maximum boost of 37.7 psi (!), which is something you’d more likely see in a truck or a thousand-horsepower tuner car. It’s gargantuan. (It also has variable-geometry vanes, for even more flexibility.) You may think that the C63’s hybrid system, which has a 204-hp electric motor, could compensate for any turbo lag, so why go through the trouble of using an electric turbo? There’s not a simple answer.
“It’s again for performance and efficiency,” Habermann says. AMG’s hybrid system uses a 6.1-kWh battery and the idea behind the control strategy is to keep the battery plenished up enough so the motor can deliver full power whenever the driver wants. By using the electric turbo to get the engine to full power quickly, the electric motor can remain on standby with energy stored in the battery. “It’s a funny thing. You have an electric traction drive, but you do not want to use it so that you can store the energy. You just want to use it for performance.”
Funny as it might be, it’s easy to see the logic when you consider that the motor on the C63’s electric turbo has just 6 kW (8 hp), so it takes a lot less energy to spin that up than it does to spin a drive motor 25 times as powerful.
AMG naturally does a lot of interesting things with the turbocharger throughout the engine’s rev range. At low engine speeds, the motor spins the turbocharger up while pressure from exhaust gasses are still building. Since this increases the volume of air going into the engine, it also increases the volume coming out, further aiding boost generation. In and around 3500 rpm and at constant throttle, the motor doesn’t do much, if anything, as there is enough exhaust gas to keep the turbocharger spinning at its maximum of 175,000 rpm. At higher speeds, up to the C63’s 7000-rpm redline, however, the motor puts out around 1 kW to keep the turbo spinning, helping extend the power band and improving throttle response. Normally turbocharged engines “die out” closer to redline, but AMG wanted a turbo engine that felt more like a naturally-aspirated one, with power building across the rev band.
As you’d expect, AMG also uses the turbo’s motor to improve transient response across the power band, and as needed. Habermann says that at lower engine speeds it can take up to a second to reach full boost pressure, in the mid-range, it’s almost instantaneous, and at high RPM, it’s around 0.4 seconds. That’s impressive for such a large turbocharger, and small enough that you don’t feel it, according to Habermann. The turbo also sends energy back to the battery off throttle during gear shifts, harnessing the air that would otherwise be sent out of a wastegate back into the atmosphere.
Spare a thought for the calibration engineers, and the guys at AMG who have to make sure the bottom end of a 2.0-liter four-cylinder doesn’t blow up in spectacular fashion when faced with 37.7 psi of boost. One also imagines the difficult task for those who designed the turbocharger’s motor as it has to spin up quickly to 200,000 rpm in an extremely hot, vibration-heavy environment.
Balis says that more automakers will embrace electric turbocharging in the near future, and not just for high-performance applications, as mild- and plug-in-hybrid vehicles become more popular and necessary. Truck manufacturers are also interested in the tech. “It’s an efficiency play, it’s an emissions play, of course, it’s also a power density play, but it’s bringing all of those benefits,” he explains. “In the end, it’s bringing a new degree of freedom to engine design that didn’t exist before…. You can kind of have air on demand with more precision.” He adds that the costs of all the hardware is coming down, making this a more viable solution for mainstream applications.
The rest depends on how our transition to fully electric motoring progresses. Perhaps e-turbos are an interim solution, but they also make internal-combustion engines more viable. It’s proof that there’s a lot more efficiency to be extracted from the internal-combustion engine.