Count’s Kustoms dips into automated deburring
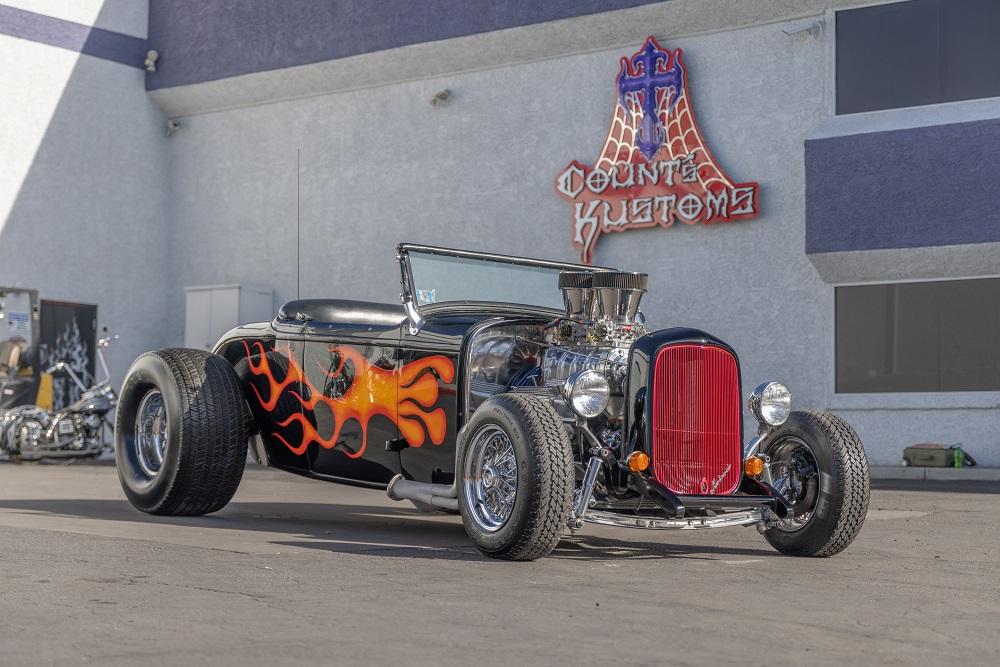
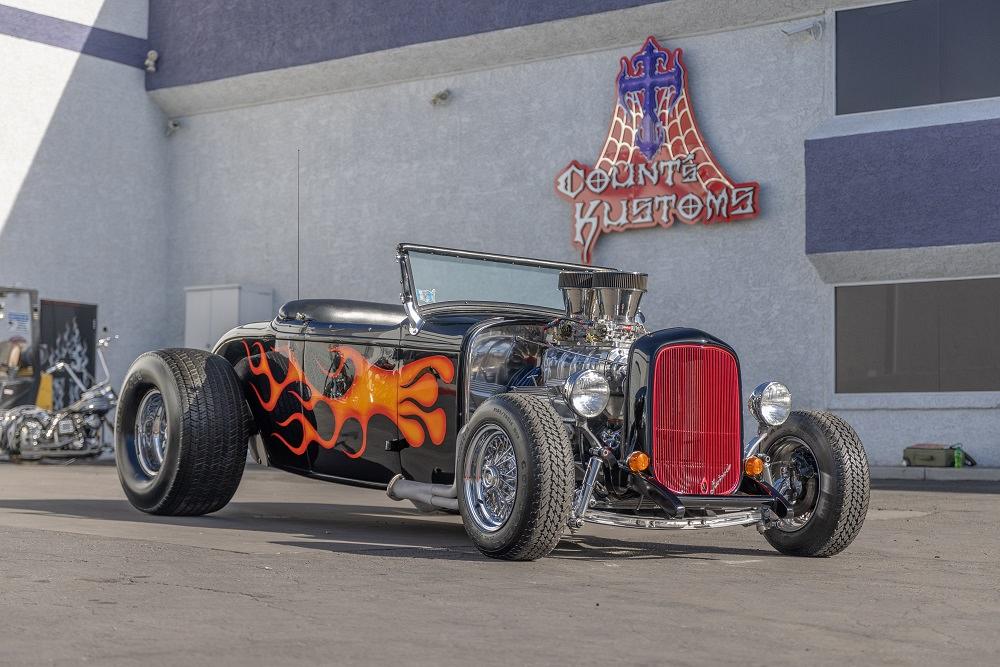
Count’s Kustoms relies on the craftsmanship of its employees, all of whom start out a automobile modification with a plan but continuously adapt. That ability doesn’t mesh properly with repetitive monotony.
It began with a metal rose and some unusual downtime. Jay LoPorto, the longtime, extensive-bearded staff and outdated-college fabrication hand at Count’s Kustoms—a warm rod and chopper store of “Counting Cars” Television present fame—had a little time on his arms, together with a bit of scrap steel.

“If you were to observe Jay make these roses, the way he does it, perfectly, it’s really barbaric.”
That was Ghetto Bob, also of “Counting Cars” fame. Equally function for Danny Koker, aka “The Rely,” the entrepreneur and identity at the rear of the Count’s Kustoms model. A lifelong auto collector, The Rely was the vehicle professional on “Pawn Stars.” The spinoff “Counting Cars” adopted, rising into a Television show airing in 163 countries. Outside of the clearly show, the Count’s Kustoms group today has about 60 personnel who work at numerous properties—not only the original very hot rod shop, but also a bar, a tattoo parlor, a museum whole of eyebrow-boosting autos, and a present shop. The reward store has plenty of Loporto’s metallic roses, painted and coated in that Count’s Kustoms glance.
“The edges are not sharp soon after he paints and clearcoats them, but they are not totally smooth either,” Bob mentioned. “I wouldn’t give one to your wife when she’s mad.”
He pointed out the edges for a bit of context up coming to the roses in the reward shop sit rows of flat metal and aluminum pieces, together with a variety of Count’s Kustoms signature cross logos—all with extremely sleek edges. Some are mounted to frames, some others are marketed individually, and all are there for hot-rod-fanatic travelers to get a very little bit of Count’s Kustoms home with them.
Most who stop by the Las Vegas operation almost certainly don’t remember the reward shop, and they possibly really do not think twice about the souvenirs, but the story at the rear of them reveals a great deal about a dilemma which is top rated of intellect for most in metal fabrication, from the largest factories to the smallest position outlets and, yes, even previous-school fabrication at a custom made warm-rod operation, English wheels and all: The place does automation make sense?
The Car Tells You
“When a client has a apparent vision, we adhere to their lead, but even then, we take distinctive paths in this article and there alongside the way, due to the fact as you progress as you perform on a motor vehicle, sometimes it tells you, ‘Go this way alternatively of that way.’ There are normally variants on the way.”
That was Koker two decades back speaking on his YouTube channel, advertising an future “Counting Cars” episode on the Heritage Channel. When he uploaded the online video, Count’s Kustoms was weathering the pandemic, a time when filming ongoing as did the operate on automobiles, but revenue from travellers efficiently halted.
As Ghetto Bob recalled, “Pre-COVID, we averaged all over 500 and 700 people a day [in the museum and gift shop]. Then we ended up shut down for two years. But we tailored, and we ended up ready to go on doing work.” By 2022, that amount recovered to about 300 a working day, and the figures have ongoing to increase into 2023. Regardless, Count’s Kustoms had (and has) fiercely faithful supporters. The shop and Television clearly show weren’t going everywhere.
All through it all, the shop’s group ongoing their function. They begin with a plan, then “listen” to the automobile as they progress by way of the challenge. They seize a plasma torch to minimize a sheet steel blank, type it with an English wheel and other hand instruments, wield a MIG gun or TIG torch, then grind and mix to realize that pristine but nonetheless handcrafted seem. “We’re all fingers-on craftsmen,” Ghetto Bob reported. “We’re aged-school in this article.”
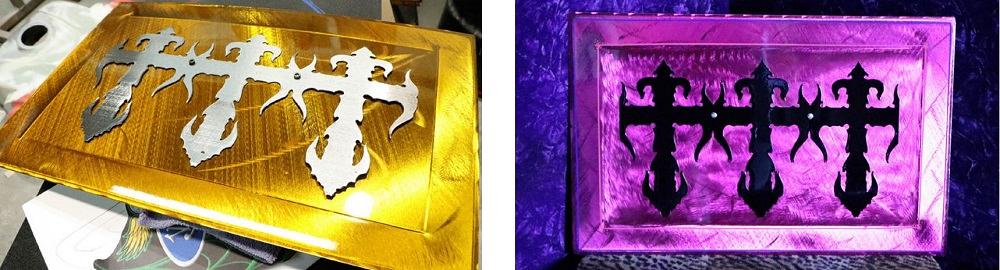
These Count’s Kustoms crosses have been plasma lower and then quickly deburred. Manual deburring took several hours and drained the shop’s sources.
Hours can be terribly extended and unpredictable as the shop’s 14 fabricators do the job to meet up with buyer deadlines or get ready a collection of autos for an impending show. Nonetheless, metalwork is their passion—and LoPorto is a primary example. In the course of downtime, he’s still performing with sheet metallic, crafting artwork like that steel rose.
LoPorto (who also sells his work through a business called Useless Coronary heart Creations) little by little expanded his steel art portfolio, and new operates began showing up in the museum present store. Then arrived other metallic parts, which includes the cross symbol and other swag. Present store sales grew, and so did the product choices. To keep up with desire, the business invested in a 5- by 10-ft. FastCut CNC plasma table, which spends its working day slicing nests of a range of flat pieces destined for the present store shelves.
Early on, the CNC plasma desk seemed like more than enough. After all, it could slash pieces extremely hard or impractical to reduce continuously and successfully by hand. Operators unloaded the parts, deburred the edges, and the minimize blanks were good to go. 
To begin with, they imagined deburring wouldn’t be an situation. Everybody realized their way all-around hand and energy tools, just after all. They employed them to put together a contoured surface for paint, to spherical edges, to put the closing glimpse on fantastical automotive creations. Surely they could handle the deburring of a number of flat blanks for the present shop.
So, they ongoing deburring the flat parts. And deburred much more. Fairly soon, people today ended up spending hrs with die grinders and other hand equipment, eradicating dross on cross logos and other styles: smaller pieces for key rings, medium-sized plates used in software organizers (with the Count’s Kustoms logo, of system), and large pieces built to be mounted on the wall.
The perform got accomplished, but it was not what the expertise at Count’s Kustoms signed up for. Edge deburring was a diverse world. The do the job wasn’t straightforward most parts experienced complex, flame-like contours and a multitude of sharp edges. Continue to, there was no creative imagination, no adapting, no “listening” to the function to see the place it requires you.
The store was turning into a disjointed hybrid. Employees targeted generally on custom made craftsmanship but endured an unwelcome dose of monotonous manufacturing. Investing hrs keeping a die grinder was a tiring, thankless position. A thing had to adjust.
And so, Count’s Kustoms invested in huge-belt deburring and graining—specifically, the Apex EZ Sander. The shop’s certain model (EZ3760M) is a solitary-head system with 37- by 60-in. abrasive belts (consequently the model title), digital abrasive belt tracking, pneumatic abrasive tensioning, and an adjustable-velocity conveyor pushed by a variable-frequency drive.
As Ghetto Bob put it, “Three passes in that device almost certainly will save an hour of human labor. The time it took to generate 1 piece, now we can produce 40.”
How Much to Automate?
“Realistically, we’re even now previous-school,” Bob mentioned. “We’re still palms-on craftsmen. In between two machines, the plasma table and the EZ Sander, there is seriously not much else we want to mass produce.”
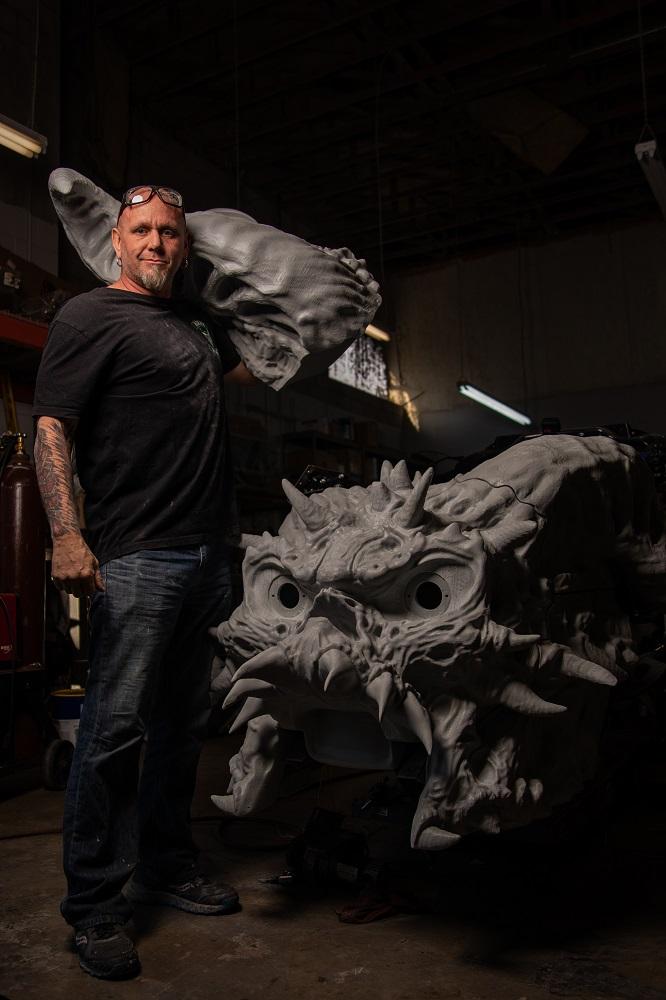
Danny “The Count” Koker doesn’t shy absent from new technological know-how, as lengthy as it can help his workforce force creative imagination to new heights—including this 3D-printed motorbike physique.
Count’s Kustoms may be previous university, but they never shy away from technologies. For instance, the organization would make use of massive-scale 3D printing to generate massive beauty adornments as well as specific automobile components. That mentioned, the technology boosts creativity it does not stifle it.
What instruments the company invests in depends on the character of the get the job done and the organization’s brand—a lesson that could apply to fabricators everywhere. Shoppers have cars and trucks modified, watch the demonstrate, try to eat at the bar, make an appointment at the tattoo parlor, and visit the museum and reward store. Why? They’re drawn to the persons in the store and their artistic electrical power. Anything at all that saps that artistic energy—like cutting and grinding a single identical flat piece just after another—is an location ripe for automation.
A personalized sheet steel fab store, though seemingly a unique earth, may possibly abide by the exact basic principle. Clients purchase from a fabricator due to the fact they rely on it can supply parts of the appropriate good quality and amount at the proper time, even in the face of extremely variable desire.
Place an additional way, customers acquire a fabricator’s capacity to address issues. Something that saps that difficulty-resolving ability—be it handbook grinding following plasma slicing, arduous tool adjustments at the press brake, or the improper components inserted in assembly—is an location well worth scrutinizing.
In the fab shop, as in Count’s Kustoms, often the occupation tells you, Go this way instead of that way. Manual or automated, no technology on the floor really should hinder that means to pay attention the occupation, change gears, and just take a new course.